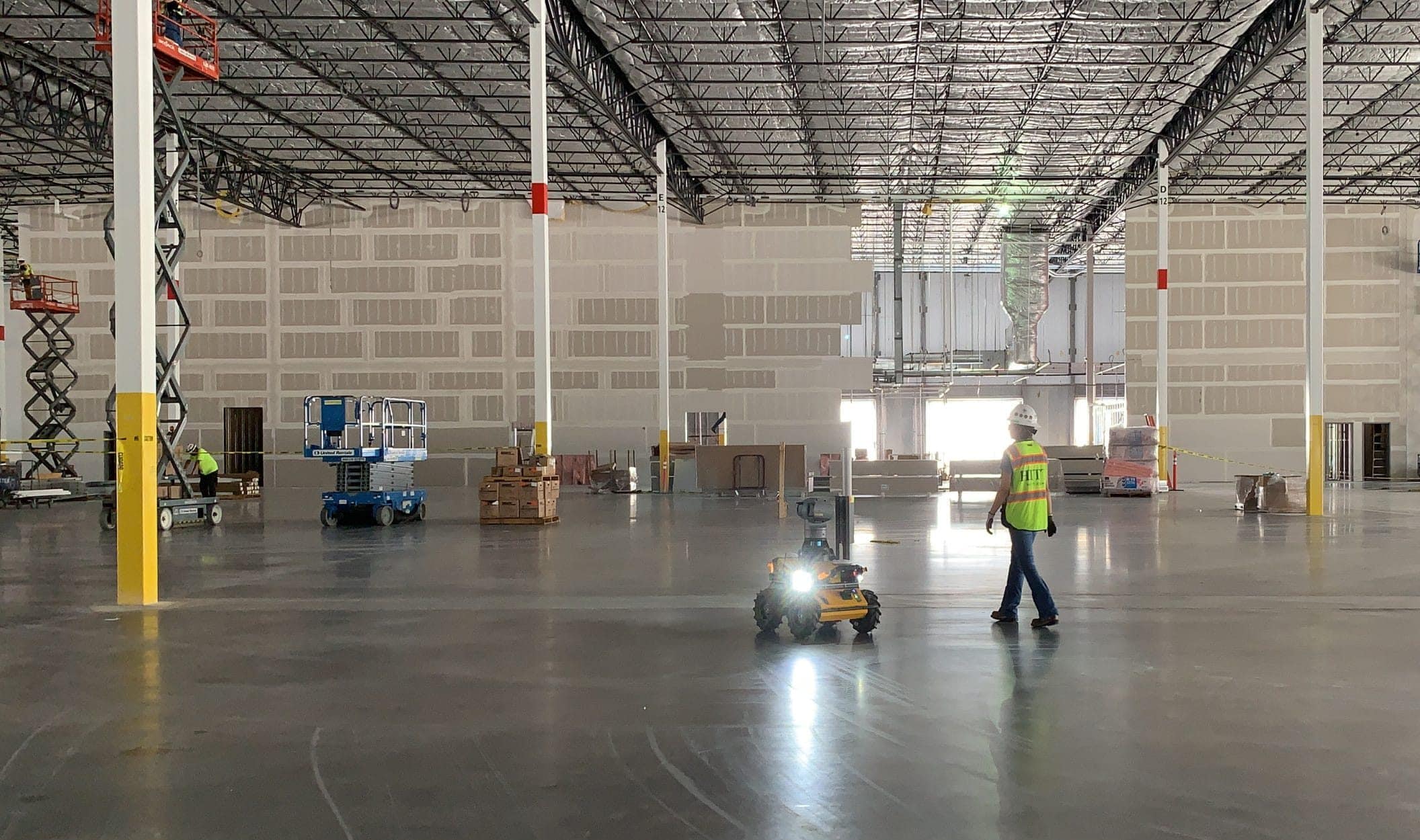
| Jan 18, 2022
Autonomous Mobile Robots on Construction Sites
Robotics can assume various roles in the construction industry both off and on-site, in the form of heavy equipment, autonomous drones, mobile robots, and more. It is an area that continues to evolve, yet can encounter a host of obstacles due to the unique and quickly changing nature of construction environments. This project aims to explore hardware options and, where necessary, develop software, with the objective of increasing productivity for construction projects. Specific tasks and trades will be explored, and partnerships with robotics experts will ensure we are leveraging the best possible solutions for the stated problems. We intend to improve team member experience, delineate safety protocols involving work alongside robotics, and validate the most favorable forms of robotics for the construction industry.
An autonomous mobile robot (AMR) refers to any robot that can comprehend and navigate its environment without needing a person to directly oversee or manage it. This is typically achieved through a complex system of computers, maps, and onboard sensors which enable AMRs to understand and interpret their environment. AMRs have made headway across various industries – manufacturing, oil and gas, military and defense, fulfillment operations, and more. However, the dynamic, ever-changing nature of construction jobsites present a uniquely challenging environment to safely and effectively operate AMRs (often termed “collaborative robots” or “co-bots”). Also of note, there is often apprehension surrounding robotics at large given the implications of their potential role in changing the future of our industry’s workforce. For the purpose of this project, our team maintains the primary function of AMRs is to work alongside humans (as opposed to replace them), augmenting productivity by carrying out repetitive or mundane tasks that would free up time on a jobsite for more skilled responsibilities.
Our Goals
The intent of this project is to explore the capabilities of AMRs and determine how they can be incorporated into a construction site workflow. We are seeking a tool that can enable superintendents to operate remotely on a jobsite, make a positive impact on jobsite experience for team members, extend the function of the superintendent, and equip site operations teams with a surveying and communication tool. Ultimately, we are investigating what technologies can equip us to accomplish these goals; believing that doing so will help address the skilled labor shortage and leverage productivity gains for targeted use cases.
AMRs operate based on a system of sensors, localization protocols, obstacle detection and avoidance, navigation, and other functions all working together in unison. Software is then layered on top of the robotic operating system (ROS), which is an open source development language for robot software (think iOS for Apple applications). Procuring the relevant hardware and developing the appropriate software for our particular use cases and workforce are paramount. We will explore various hardware options within the framework of the unique, often highly specific and changeable movements required on a construction jobsite. Agility is key and will dictate the hardware selected. The same considerations will be applied when developing software specific to the construction industry. Specific trades and tasks will be explored, and HITT will partner with robotics experts to ensure we are leveraging the best possible solutions for the stated challenges.
HITT has determined target points for a pilot program for this specific use case, and partners will be selected to align with requirements that we need to comply with on ever-changing jobsites.
Ultimately, we expect to validate various forms of robotics for the construction industry, delineate safety protocols while working alongside robotics, and incorporate our research and developments into an improved, more efficient team member experience.
Key Findings
- Different navigation technology is required for indoor and outdoor mobility – this poses a specific problem to solve for when deployed on a construction jobsite.